お客様の「感動」を「つくる」ことを目的とした、
旬の情報満載の販促・マーケティング系コンテンツです。
Idea4U コンテンツ
「工場のデジタル化」で変革する 生産現場の数値化から導き出される設備総合効率OEEと新たなメリットとは?
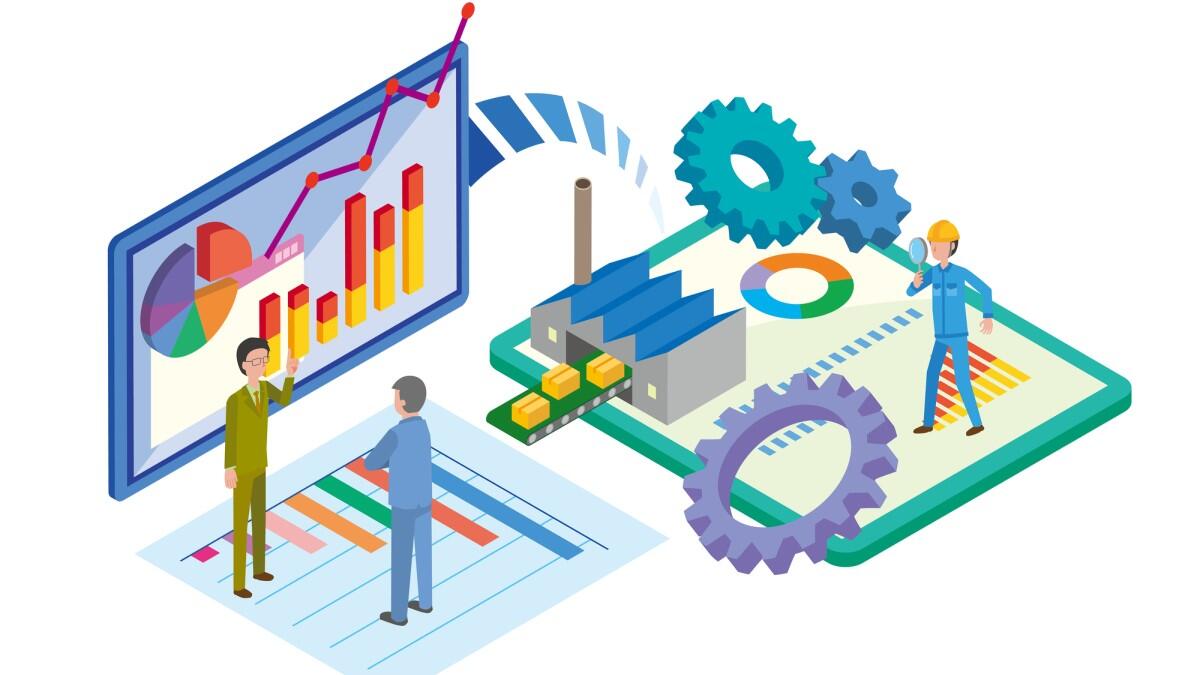
改めて実施すべき生産現場の数値化
新型コロナの影響により、ビジネス環境における急速な変化に対応するため様々な改革を求められています。生産現場においても、生産性向上のための取り組みを日々行なわれていますが、さらに成果を出すためにはDX(デジタルトランスフォーメーション)の考え方を取り入れて「攻め」のモノづくりを実践しないといけなくなりました。
具体的には、これまでの生産性向上の多くは、1つの作業に対してどれだけ短縮できるかという手法ありきの側面が強く、手順を変化させたり、機械を導入させることで実現してきました。ただ、目先の生産性や人の感覚値を重視するあまり、生産性の阻害要因(機械の停止、機械や作業の速度低下、作り直し)の詳細をデータ取得等で解決させる動きはあまり浸透しませんでした。この動きが浸透しなかった最大の理由は、データを人力で取得するしかなかったか、あるいは取得できていたとしてもデータ連携してその後の活かし方がイメージできなかったかもしれません。今はIoT(Internet of Things)でモノとデータが繋がりやすくなり、必要なデータもセンサー等で収集しやすくなりました。
では、どんなデータを取得すべきでしょうか?先程の阻害要因から考えて、機械に対して全体の「開始時間」「終了時間」はもちろん、「段取り時間」や「生産時間」は必要でしょう。また「テスト時間」や「停止時間」も把握すべきですし、エラーになった「番号」や「不良数」を取得しやすくする必要があります。あと、重要なのは、その作業を「誰」が対応したかを把握することで、スケジューリングにおける人員配置の最適化などにも有効になりそうです。
注目すべき設備総合効率OEEとは
最近改めて注目されているのが、設備総合効率OEE(=Overall Equipment Effectiveness)という生産設備の稼働効率における指標です。元々は、トヨタ生産方式をマサチューセッツ工科大学が体系化・一般化したリーン生産方式がありますが、その重要指標の1つにOEEがあります。OEEは、可動率(※)、性能、品質の3つの測定可能なところで生産効率を確認します。計算式にすると、OEE=可動率×性能×品質とされ、多くの業種で目標として85%程度の値が掲げられております。
・可動率=スケジュールの稼働予定時間のうち、実際に設備が稼働している時間の割合
・性能=生産設備の設計(工程)上の製造速度に対する実際の製造速度の比率(工程効率)
・品質=全生産数に対する良品数の割合(良品率)
(※)「稼働率(かどうりつ)」と「可動率(べきどうりつ)」の違い
「稼働率」は設備の生産能力に対してどのくらい生産できたかを示す指標に対し、「可動率」は製造したい時にすぐに製造できるかどうか?を示す指標です。生産性を向上させる目的は同じですが、「稼働率」は機械を稼働することが可能であった割合であり、生産数量によって影響を受けます。一方、「可動率」は停止要因に影響を受けるもので、機械を動かしたい時に正常に動かせた割合となります。
例えば可動率が90%、性能が95%、品質が98%だとすると、OEEは83.8%となります。このOEEを低下させる阻害要因として、以下8つの項目が挙げられています。
①可動停止要因
(1)機械の故障または不備(ドカ停)、(2)切替のための設定・調整、(3)刃具の交換、(4)立ち上がりのロスの4つの要因が挙げられます。(1)については、機械の突発的な故障が該当します。(2)や(3)については、品種や工程内容の変更によって都度機械を止めないといけない事が該当します。また切替による確認作業や掃除なども含みます。(4)については、機械を起動させる際の時間的なロスによる悪化です。主にはスタートアップ時に生じる生産条件(温度・湿度・流量・粘度等)待ちや、そもそもの部材待ちなどがこれに該当します。
②性能要因
(5)短時間の設備停止(チョコ停)、(6)速度低下によるロスの2つの要因が挙げられます。(5)については、例えば部品が詰まったり、搬送が停滞したりなどのちょっとしたトラブルの積み重なりが該当します。(6)については、機械そのものの都合による減速や要員の不慣れによるスピード低下がこれに該当します。
③品質要因
(7)不良品発生、(8)手直しによるロスの2つの要因が挙げられます。(7)については修復不可能なものであり、単純に再生産するロスが該当します。(8)については、修復可能なものであり、修復するための手直しのための作業ロスが該当します。
OEEの考え方から見えてくる「人時生産性」と「標準作業時間」
OEEは、機械の稼働時間に対して良品が製造できた時間比率についてを表します。これを1人1人の作業者に置き換えて、OEE同様に人の就業時間から良品が製造できた時間比率のことを人時生産性といいます。一見、1人1人の能力だけに目を向けてしまいそうですが、そうではなく1人1人を適所に配置し、利益を増やし、総労働時間を減らして効率化させることが目的になります。
また、OEEと人時生産性が見えてくると、機械における標準作業時間が割り出せるようになります。さらには、作業によっては難易度が異なり場合もあるので、品目によってはその比重なども明確にできそうです。そうすると、これまで「人件費」「製造経費」のざっくりした部分が、「標準作業時間×難易度(係数)×人件費×数量」で計算できるようになります。これにより、これまでのコスト換算(見積金額)が本当に適正なのかを見直すこともできます。
このように、まだまだ見え隠れする潜在的な生産課題においては、データを取得して可視化をする「工場のデジタル化」が求められます。可視化することで全体だけでなく、どこに改善すべきボトルネックが潜んでいるかが分かり、これまで出来なかった生産改善や最適化、さらには作業者1人1人の安全性確保やモチベーション向上にもつながるでしょう。
(株式会社フジプラス)
まとめ
■データ取得においては、項目を洗い出し、極力人の手間のかからない方法を考える。
■OEEを理解することで、工程におけるボトルネックが把握できる。
■OEEは「人」の最適化や「利益」の増加、安全性確保やモチベーション向上につなげることができる。
あなたにオススメのコンテンツ
- DX
メーカー発で新たな「価値」を届ける DtoCの取り組みがもたらす いま必要とされるモノづくりの変化について
2023年10月 3日 NEW - DX
「分散型社会」に対応する 誰もが参加可能な自走型コミュニティを実現させる 自律分散型組織DAOとは
2023年6月21日 NEW - DX
「デジタルアート」だけではないNFT ビジネスで幅広く活用できる NFTの新たな「体験」や「価値」とは
2023年5月22日 NEW - DX
「ホンモノ」や「オリジナル」に価値がある ドロップシッピングが生み出すマッチングによる新たな価値提供
2023年3月10日 NEW - DX
DXプロジェクトを例に考える メンバー全員で成功させるためのプロジェクトマネジメントとは
2022年11月 2日 NEW - DX
変化の時こそチャンスに備える! 動きを止めずにビジネスを加速させる社内DX事例のご紹介
2022年4月 8日 NEW - DX
ブロックチェーンが社会や市場を変える ブロックチェーン技術におけるスマートコントラクトの概念とNFTの価値とは
2021年11月 4日 NEW - DX
厳しいビジネス環境を乗り越えるために パートナーシップで取り組むBPOとアウトソーシングとの違いとは
2021年9月15日 NEW - DX
業務改善から業務変革へ BPM視点で見直す業務マニュアルによる可視化とDXの必要性
2021年7月 7日 NEW - DX
双方のビジネスを成功させるための契約書 ITサービスを支援するデジタル印刷連携におけるSLAの意義とは
2021年6月 9日 NEW - DX
アフターデジタルを考える コミュニケーションの変化によるメディアの再定義と求められる提供価値とは
2021年4月21日 NEW - DX
デジタル印刷が空想と夢への懸け橋に! 世界で1冊だけのパーソナライズ絵本 「感動体験」を仕掛ける絵本DX
2021年3月17日 NEW - DX
「工場のデジタル化」で変革する 生産現場の数値化から導き出される設備総合効率OEEと新たなメリットとは?
2021年3月17日 NEW - DX
データを「溜める」から「繋げる」で変革を ビジネスを加速させる切り札となる商品情報管理PIMとは
2021年2月17日 NEW - DX
変化を察知し議論~施策実行を加速させる データの可視化から分析・判断を素早くするためのBIツールについて
2021年1月27日 NEW - DX
DX(デジタルトランスフォーメーション)イノベーションを「人」で実現させるための戦略的な組織改革とは?
2021年1月13日 NEW - DX
DX(デジタルトランスフォーメーション)スマートファクトリー化で「攻め」の製造現場づくりを考える
2020年11月18日 NEW - DX
DX(デジタルトランスフォーメーション)人やITの分断解消で変革できる事務処理のこれからの常識とは?
2020年9月30日 NEW - DX
DX(デジタルトランスフォーメーション)複雑化した「リアル」と「デジタル」における コミュニケーションの最適化
2020年7月29日 NEW - DX
DX(デジタルトランスフォーメーション)データ蓄積と可視化から仕組みをつくるこれからの「売らない営業」とは?
2020年7月 1日 NEW - DX
DX(デジタルトランスフォーメーション)既成概念を見直し、これからの時代に対応するための「仕組み」づくりについて
2020年7月 1日 NEW